Electrostatic discharge (ESD) poses a hidden threat to LED chips, causing significant damage without visible signs. These highly sensitive components are vulnerable to static electricity, which can trigger immediate failures or long-term performance issues. During manufacturing, storage, or handling, ESD can undermine LED reliability and lifespan, leading to costly repairs or product defects.
This blog explores practical steps to prevent ESD damage, emphasizing best practices for LED chip storage and handling. We’ll examine ESD risks, their impact on performance, and effective methods to protect sensitive components. We’ll also discuss restoring LEDs exposed to static discharge and highlight our solutions to safeguard your investments.
By adopting these guidelines, you can ensure LED chip longevity and reliability, avoiding the costly consequences of static damage.
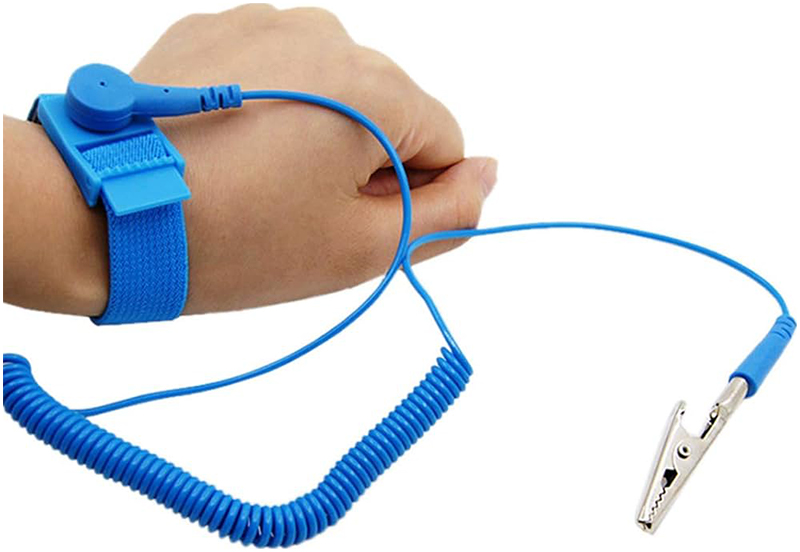
Understanding Electrostatic Discharge (ESD) and Its Risks
To effectively protect LED chips, understanding electrostatic discharge (ESD) and its risks is crucial. ESD can silently damage these sensitive components, impacting performance and reliability. This section explores what ESD is, its common sources, and why LED chips are particularly vulnerable, providing the foundation for implementing robust prevention strategies.
What Is ESD and Why Does It Matter
Electrostatic discharge (ESD) happens when an electrical charge transfers between objects, often during contact or proximity. Common in electronics environments, ESD poses a serious threat to sensitive components like LED chips. These delicate devices, with intricate internal structures, are highly susceptible to static electricity. Even an invisible static shock can harm an LED chip, burning out or disrupting its circuits, causing failures or malfunctions. Controlling static buildup during LED chip handling and storage is vital, as ESD can lead to costly damage and reduced performance.
Common Sources of ESD in LED Handling
ESD risks arise from multiple sources during LED chip handling. The human body, a primary culprit, accumulates static charge through movement or friction, especially in dry conditions. For example, walking on a carpet or handling materials without grounding can generate thousands of volts, risking chip damage upon contact. Non-ESD-safe tools, such as standard tweezers or pliers, also increase ESD risks if not designed to prevent static. Additionally, low-humidity environments exacerbate static buildup, as dry air heightens the potential for ESD events.
Why LED Chips Are Vulnerable
LED chips are particularly prone to static damage due to their sensitive internal components. Fine bonding wires and complex wafer structures are easily harmed by even minor static electricity. A single ESD event can cause complete chip failure or long-term issues, like diminished brightness or a shortened lifespan. Given their fragility, implementing strict precautions during handling and storage is essential to minimize ESD-related damage risks.
How ESD Impacts LED Chip Performance
Electrostatic discharge (ESD) can severely impact LED chip performance, causing immediate or gradual damage. From electrical failures to optical issues, ESD compromises reliability and quality. This section examines how ESD affects LED chips, highlighting electrical, optical, and lifespan challenges to underscore the need for effective prevention measures.
1. Electrical Failures from ESD
Electrostatic discharge (ESD) triggers significant electrical failures in LED chips. When static electricity strikes a chip, it forms sudden conductive paths within its circuitry, leading to short circuits or leakage currents. These issues can instantly damage the LED, impairing its functionality and risking complete failure. Though often invisible, this damage undermines performance, causing reduced light output, power instability, or total chip failure. Proper precautions during LED chip handling are essential to prevent ESD and avoid these costly breakdowns.
2. Optical Degradation
ESD also causes optical degradation in LED chips. Static discharge can harm the phosphor coating or optical layers critical for light emission, reducing light output and making the LED dimmer and less efficient. Additionally, ESD may shift the chip’s color temperature—for instance, turning blue light to yellow due to phosphor damage—resulting in inconsistent color quality. Such degradation impairs LED performance and affects final product quality, particularly in applications requiring precise color consistency.
3. Reduced Lifespan and Costly Failures
Beyond immediate damage, ESD significantly shortens LED chip lifespan. Even minor static discharge can inflict microscopic damage to internal components, causing gradual performance decline. Affected LEDs fail sooner, necessitating frequent replacements. Industry estimates suggest ESD accounts for 30% of field failures, driving costly recalls and rework. These failures inflate operational costs and risk reputational harm. Preventing ESD is vital to extend LED chip lifespan and minimize expensive failures and returns.
Best Practices for ESD-Safe LED Chip Storage
Effective storage practices are vital to shield LED chips from electrostatic discharge (ESD). By adopting proven methods, you can minimize static risks and ensure chip reliability. This section outlines key strategies for creating a robust ESD-safe storage system for your LED chips, from specialized packaging to environmental controls.
1. Using ESD-Safe Packaging
Protecting LED chips from electrostatic discharge (ESD) starts with proper packaging. ESD-safe bags and conductive trays are critical for safeguarding chips during storage and transport. These materials block static charges, preventing harmful static buildup. Storing chips in ESD-safe bags creates a protective barrier, reducing ESD damage risks. Conductive trays ensure a static-free environment, shielding delicate internal circuits from charge buildup. Always choose packaging that meets industry standards to maximize LED chip protection.
2. Controlling Storage Environment
A controlled storage environment is essential to prevent ESD damage to LED chips. Maintaining relative humidity (RH) between 40-60% minimizes static buildup, as dry conditions increase electrostatic discharge risks. Using a humidifier in overly dry areas helps sustain optimal humidity levels. By regulating temperature and humidity, you establish a stable environment that guards chips against ESD and other environmental threats.
3. Implementing Grounding Measures
Grounding is a cornerstone of ESD protection. All storage racks, shelves, and workstations must be grounded to dissipate static charges safely, preventing harm to LED chips. Employees should wear grounding wrist straps to avoid transferring static from their bodies. ESD-safe flooring further reduces static buildup. These measures foster a static-free environment, crucial for preserving the integrity of sensitive LED chips.
4. Regular ESD Audits
Regular ESD audits are key to sustained protection against ESD damage. Monthly audits identify risks or weaknesses in ESD control measures, ensuring equipment, packaging, and environments meet standards. Checking for damaged ESD-safe bags, faulty grounding, or low humidity catches issues early. Audits maintain compliance with ESD safety standards and enable adjustments to enhance chip protection, ensuring long-term product reliability and avoiding costly issues.
Safe Handling Practices to Prevent ESD Damage
Safe handling of LED chips is critical to prevent electrostatic discharge (ESD) damage. Proper techniques and tools can significantly reduce static risks, ensuring component reliability. This section details essential practices, from personal grounding to staff training, to maintain an ESD-safe handling environment for LED chips.
1. Personal Grounding Techniques
When handling LED chips, operators must be grounded to prevent static electricity from reaching sensitive components. Wearing an ESD wrist strap is a highly effective method, safely dissipating built-up static from the body. Additionally, avoid synthetic clothing, which generates static easily, and opt for natural fibers to minimize static buildup. Personal grounding is vital for reducing ESD damage risks, keeping LED chips safe during handling.
2. Using ESD-Safe Tools and Workstations
Using ESD-safe tools and workstations is essential for static-sensitive environments. ESD-safe tweezers, made from non-static materials, prevent static charge transfer to LED chips, eliminating a key ESD risk. ESD-safe workstations, equipped with grounding mats and protective features, dissipate static charges, ensuring a safe handling environment. These tools and setups are crucial for proper LED chip handling during assembly, testing, or packaging.
3. Training Staff on ESD Protocols
Proper equipment alone isn’t enough—staff must be trained on ESD handling protocols. Training ensures employees understand ESD prevention and follow best practices for LED chip handling. This includes correctly using wrist straps, ESD-safe tools, and maintaining a static-free environment. Regular training and clear procedures, covering storage and ESD threat identification, reinforce these practices. Educating staff fosters a safety culture, protecting components and preventing costly errors.
Recovering from ESD Damage: Is It Possible?
Recovering from electrostatic discharge (ESD) damage in LED chips is challenging, as static damage is often permanent. Understanding the extent of damage and when recovery is feasible is key. This section explores how to assess ESD damage, decide when to discard chips, and recognize recovery limitations to ensure product reliability.
1. Assessing ESD Damage
After an ESD incident, promptly assess whether the LED chip is damaged. Conduct a thorough inspection for failure signs, such as short circuits, discoloration, or reduced light output. Use a multimeter to detect short circuits, indicating irreversible damage. Check light output for significant drops, another clue of internal ESD damage. Note any visible discoloration, like color shifts or dimming, as these suggest the chip may no longer perform reliably.
2. When to Discard Damaged Chips
Severe ESD damage is often permanent, necessitating chip disposal. If the LED chip shows over 20% light output loss or permanent electrical failure, such as a short circuit, discard it. Using damaged chips risks poor performance, shorter lifespan, and end-product failures. If the chip fails to meet specifications due to static damage, recovery isn’t viable. Discarding defective chips prevents production issues, ensuring only reliable, functional components are used.
3. Limitations of Recovery
Unlike moisture damage, which may be reversed through drying or baking, ESD damage is rarely recoverable. Static electricity often causes irreversible harm, especially with short circuits or significant light output loss. Prevention is the most effective strategy. Proactive measures to shield LED chips from static discharge avoid permanent damage, ensuring product longevity and performance while minimizing costly ESD-related failures.
Protect Your LED Chips with Us
Electrostatic discharge (ESD) threatens the performance and reliability of LED chips. Even a minor static shock can cause irreversible damage, resulting in electrical failures, diminished brightness, and reduced lifespans. Prevention is crucial to mitigate these risks, with proper handling, storage, and ESD-safe materials serving as vital safeguards for your LED chips.
At Siro Electronics, we recognize the paramount importance of ESD protection. Our expert solutions, including data sheets, samples, and customized advice, empower you to adopt best practices for LED chip storage and handling, ensuring your components remain safe and reliable throughout their lifecycle.
Don’t let static damage undermine your products. Contact us today to enhance your LED projects and secure your investments with cutting-edge LED component solutions.