LED chips power modern lighting and electronics, driving automotive, healthcare, consumer electronics applications, and beyond. From vehicle lighting to medical devices and smart home systems, these compact semiconductors offer exceptional performance, efficiency, and durability. Yet, their sensitivity to handling and storage demands careful attention. Mishandling during transport, improper storage, or incorrect installation can reduce light output, shorten lifespan, or cause outright failure.
Upon receiving your order of LED chips, the very first step is to carefully inspect the shipment for completeness and any visible damage. Any defects or discrepancies should be addressed immediately by contacting your supplier. Promptly resolving such issues will ensure that you don’t face delays or additional costs.
Such issues can raise costs and disrupt project timelines, frustrating manufacturers and end-users alike. With LEDs increasingly vital to critical applications, ensuring their reliability is paramount.
This article outlines ten essential practices for safely handling and storing LED chips. These best practices will help you maximize their performance and longevity, avoiding the costly pitfalls of poor handling and keeping your projects on track.
Let’s explore these actionable tips to protect your LED chips from the start.
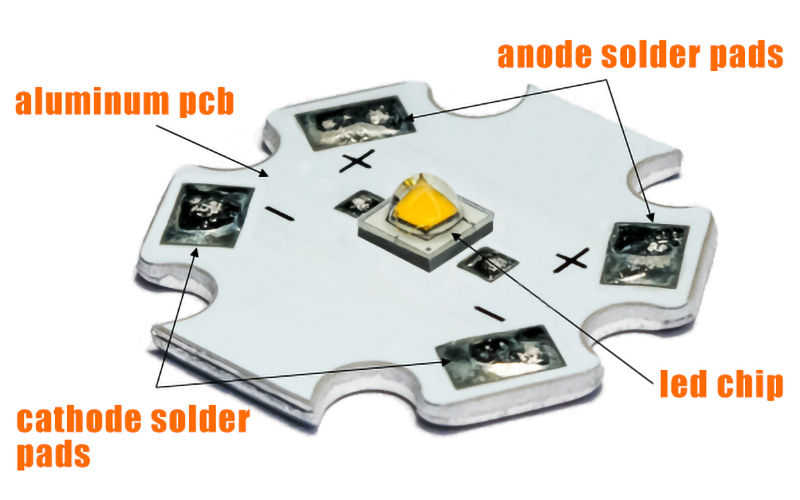
1. Protect Your LED Chips from Electrostatic Damage
Electrostatic discharge (ESD) poses a major threat to LED chips. Even a minor static shock can trigger immediate or latent failures, compromising performance and lifespan. As LED chips are highly sensitive to electrical interference, ESD can damage internal components, causing subtle malfunctions or early degradation that may go unnoticed initially.
To minimize ESD risks, adopt strict precautions during handling and storage. Equip your workspace with anti-static tools, such as grounded mats and wrist straps. Always wear an ESD wristband to safely dissipate static buildup from your body.
Additionally, store LED chips in ESD-safe packaging, like conductive bags or containers, to prevent static accumulation during transport and storage. Avoid handling chips near static-prone materials, such as plastics or unground surfaces.
By implementing these measures, you’ll significantly reduce ESD-related failures, prolong LED chip lifespan, and keep your projects running smoothly. ESD protection is a small investment with substantial long-term benefits.
2. Maintain Optimal Storage Conditions for LED Chips
LED chips are sensitive to environmental factors, and improper storage can significantly degrade their performance. High humidity or extreme temperatures can damage LED internal components, causing reduced light output, color shifting, or complete failure. It’s essential to maintain optimal storage conditions to ensure reliability and longevity.
Keep LED chips in an environment between 5°C and 30°C with humidity below 60%. This prevents moisture from entering the components and avoids temperature changes that harm performance. Store chips in moisture-proof cabinets or containers to maintain a controlled environment and protect against excess moisture.
Moisture sensitivity levels (MSL) are critical for handling LED chips. Each chip has an MSL rating, showing how long it can be exposed to ambient humidity before needing baking. For example, MSL 5a chips must not be exposed for more than 24 hours without re-drying to maintain their integrity.
For instance, an automotive company stores LED chips in a climate-controlled room with desiccants and hygrometers. This approach led to no moisture-related failures for years, supporting their high-performance lighting systems.
By controlling temperature and humidity with tools like desiccants and hygrometers, you can preserve LED chip quality and avoid performance issues.
3. Solder LED Chips Correctly to Avoid Damage
Improper soldering can cause permanent damage to LED chips, resulting in poor performance or complete failure. Overheating during soldering is a common risk, as excessive heat may harm the LED’s internal structure, including the bonding wire and wafer material, causing reduced efficiency, color shifts, or failure. To prevent these issues, it’s essential to follow the soldering guidelines provided in the chip’s datasheet.
Always check the datasheet for the recommended soldering profile. For example, many LED chips allow a maximum of 260°C for 3 seconds to avoid thermal damage from heat exposure. Using reflow soldering is advisable, as it ensures even heat distribution and reduces localized overheating risks.
To optimize soldering, test samples before full production to catch issues early. Using lead-free solder and reflow ovens aligns with IPC soldering standards, ensuring reliable, high-quality solder joints.
By following proper soldering guidelines and using suitable equipment, you can minimize overheating risks and boost the longevity and reliability of your LED applications.
4. Ensure LED Chip Compatibility with Drivers
Driver incompatibility is a common issue with LED chips, causing flickering, reduced performance, or complete burnout. LED chips require specific voltage and current ranges, and a mismatched driver can lead to malfunctions. Issues like voltage spikes, unstable current, or insufficient power can shorten chip lifespan or cause early failure.
To ensure proper operation, match the LED chip’s forward voltage and current needs with the driver’s output. For example, an LED chip needing 2.8-3.2V and 350mA requires a driver delivering that voltage and a constant 350mA current. Constant-current drivers are key, as they stabilize current to prevent overdriving and ensure reliable performance.
Before mass production, test prototypes with the chosen driver to confirm compatibility and avoid performance problems. Use a multimeter to check the driver’s voltage and current output, ensuring they meet the LED chip’s requirements.
By confirming driver and LED chip compatibility, you can prevent issues like flickering and burnout, ensuring top performance and long-lasting LED products.
5. Implement Effective Thermal Management
Heat poses a major threat to LED chip performance and longevity. Overheating reduces efficiency, causes early failure, and shortens chip lifespan. As LED chips convert electrical energy into light, they generate heat that must be dissipated effectively to maintain optimal performance. The junction temperature, at the chip’s base, is critical—if it exceeds 85°C, it can cause permanent damage.
To manage heat risks, adopt proper thermal management strategies. Heat sinks are highly effective, increasing surface area to spread and dissipate heat evenly into the environment. Thermal pads improve heat transfer between the chip and heat sink, boosting dissipation further.
Monitoring junction temperature is essential. Use thermal sensors to ensure it stays within safe limits. Consider the LED package’s thermal resistance, which affects heat flow from the junction to the surroundings. Lower thermal resistance improves heat dissipation efficiency.
By applying effective thermal management, you can maximize LED chip lifespan and performance, delivering lasting value to your projects.
6. Handle LED Chips with Care
Mechanical stress is a common cause of LED chip damage during handling. Even minor impacts or improper handling can cause cracks, misalignment, or broken components, harming performance and lifespan. Due to their delicate nature, LED chips require careful handling to prevent such damage.
Use proper tools like tweezers or vacuum pickups when handling LED chips. Non-slip tweezers enable precise placement without excessive pressure. Vacuum pickups are ideal for moving small, fragile components, avoiding mechanical stress. Both tools minimize direct contact with the chip’s surface, protecting sensitive areas like bond wires.
Always store and transport LED chips in their original packaging, designed to shield against mechanical and environmental damage, keeping chips intact until use.
LED package types, such as SMD and COB, vary in fragility. SMD LEDs, with small sizes and thin leads, are more prone to damage, while COB LEDs, though sturdier, still need careful handling to protect bonding wires.
By using the right tools and methods, you can keep LED chips in top condition, ensuring reliable performance and long lifespan.
7. Protect LED Chips from Chemical Exposure
LED chips are highly sensitive to chemical exposure, which can cause corrosion, discoloration, or early failure. Volatile organic compounds (VOCs), sulfur compounds, and outgassing from adhesives or coatings can harm performance by reacting with the encapsulant or metal contacts, leading to chip darkening, adhesion loss, or electrical shorts.
To shield LED chips from chemical contamination, follow strict handling and storage protocols:
- Avoid Solvents and Fumes: Keep LED chips away from cleaning agents, adhesives, or chemicals emitting harmful vapors. Use non-corrosive materials and ensure good ventilation when working with chemicals near LEDs.
- Use Cleanroom Protocols: Employ cleanroom environments to control chemical and particulate contamination. Cleanrooms with filtered airflow reduce airborne contaminants that could damage LED components.
- Check Storage Areas: Regularly inspect storage spaces for outgassing materials or improperly stored chemicals. Maintain a clean, controlled environment to prevent exposure to harmful substances.
By following these practices, you can protect LED chips from contamination, ensuring long-lasting, reliable performance across applications.
8. Regularly Inspect Stored LEDs
Long-term storage of LED chips can cause degradation, leading to poor performance or failure in critical applications. Environmental factors like temperature fluctuations, humidity, and light exposure may trigger color changes, reduced brightness, or component corrosion. Regular inspections are essential to maintain optimal performance.
Test LED batches every six months for signs of degradation, such as discoloration, corrosion, or lower efficiency. Using a First-In, First-Out (FIFO) system ensures older stock is used first, preventing chips from degrading due to prolonged storage.
Key Considerations:
- Degradation Risks: Stored LEDs may lose efficiency or discolor, impacting performance.
- Inspection Tools: Conduct visual checks and use test rigs to measure light output.
- Storage Life: LED chips typically have a 2-year shelf life, so regular testing catches issues early.
By conducting regular checks, you can protect against degradation, maintain high-quality products, and extend the lifespan of stored LED chips for reliable project outcomes.
9. Safeguard LED Chips During Internal Transportation
Internal transportation, such as moving LED chips from the warehouse to the production floor or external processors, is a critical stage where chips are vulnerable to damage. Improper packaging or handling can expose them to electrostatic discharge (ESD), mechanical shock, or moisture, causing immediate or long-term performance issues. Proper packaging is essential to protect chips during these movements.
Use ESD-safe trays and reels to prevent static build-up, which can permanently harm sensitive components. Employ shock-resistant packaging and moisture barriers to shield chips from impacts and humidity, avoiding cracks or corrosion.
Clearly label packages with handling instructions to ensure workers understand the chips’ sensitivity and follow gentle handling and storage guidelines.
For example, an automotive supplier faced chip damage during internal transport, causing production delays. By adopting shock-resistant trays, ESD-safe reels, moisture-proof packaging, and clear labels, they cut damage by 10%, ensuring a smooth workflow and lower costs.
10. Leverage Supplier Support and Datasheets
Misreading LED chip specifications can cause poor performance, inefficient applications, and higher project costs. Key specifications, like luminous flux, wavelength, and forward voltage, determine a chip’s suitability for specific uses. Misinterpreting these can lead to underperforming systems, color mismatches, or early failure.
Always review the supplier’s datasheets, which detail electrical characteristics, thermal management needs, and optimal operating conditions. Understanding these ensures LEDs operate within recommended limits, boosting lifespan and performance.
Additionally, seek technical support from suppliers. Their expertise helps select the right chips or troubleshoot issues for your application.
By using datasheets and supplier expertise, you can choose and use LED chips correctly, improving performance and avoiding costly errors.
Ensure LED Chip Success with These Practices
In summary, the ten best practices outlined are vital for ensuring the reliability, longevity, and success of your LED chip projects. From safeguarding against ESD and controlling storage conditions to proper soldering and driver compatibility, each step optimizes performance and prevents costly issues.
By adopting these practices, you can boost efficiency, cut costs, and improve product quality across applications like automotive lighting, medical devices, or consumer electronics. Proper handling, thermal management, and regular inspections preserve LED integrity, extending lifespan and enhancing project outcomes.
We strongly recommend integrating these tips into your workflow for optimal results. For tailored guidance, consult experts or contact your LED supplier with specific needs.
By following these practices, you can achieve peak LED chip performance, ensuring lasting success and greater project value.
Get Started with Your LED Chips
Ready to enhance your LED projects? Request samples, download datasheets, or contact us today for personalized advice and the best solutions for your needs. Let’s work together to ensure optimal performance and long-term success for your applications.